Fixed material loading system
The quantitative control system consists of quantitative blanking electrical control cabinet, monitoring system and quantitative blanking upper computer program.
Classification:
Fixed material loading system
Key words:
E-mail:
system composition
The quantitative control system consists of quantitative blanking electrical control cabinet, monitoring system and quantitative blanking upper computer program.
System process
The vehicle is aligned with the blanking port, the driver swipes the card, and the upper computer system manually or automatically turns on the blanking switch according to the load weight in the card. After the vehicle is loaded to the load tonnage, the system automatically cuts off power and closes the blanking port. The upper computer saves the data, the vehicle weighs down and the loading is completed.
Unattended Management System Description
System Overview
According to the actual business scenarios and information needs to form a set of information system integration solutions, through information technology to strengthen the enterprise's sales of materials, finance and other processes of management. With the help of electronic tags and license plates, the system pre-encrypts order information, vehicle information, weighing information and silo blanking information in advance to prevent the leakage of sensitive data, tighten the operation process, eliminate human omissions and fraud, optimize the allocation of enterprise resources, and minimize operating costs.
The system is divided into several management modules: A8 information platform, license plate recognition system, two-dimensional code recognition system, ID card reader, electronic fence queuing management, entrance guard management, automatic control module, unattended weighing management, quantitative loading management, source control management, etc.
System Design
1, Sales Pound Process Design
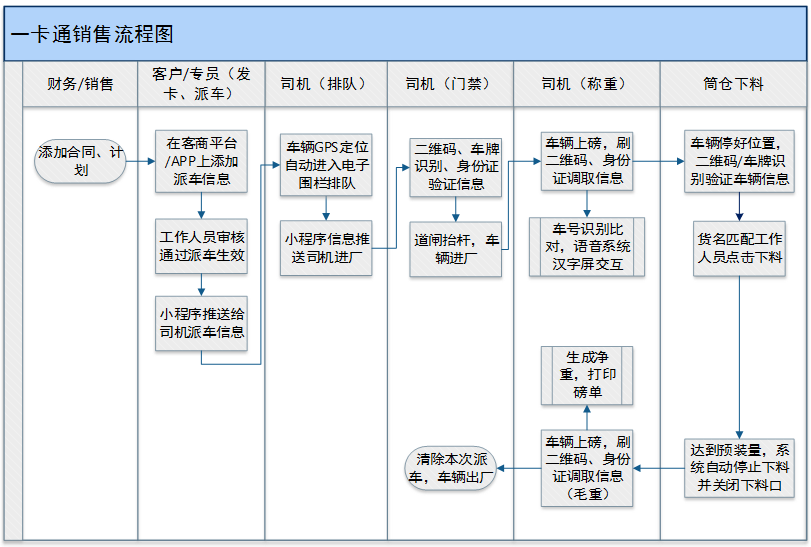
The process is described as follows:
1. Add contract plan: relevant staff add large contracts and short-term order plans on the management platform.
2. Vehicle Registration: Fixed vehicle registration license plate number information and bound WeChat applet.
3. Add dispatch: Staff or transportation company or customer add dispatch information on the management platform (or applet).
4. Queue management of electronic fence: when the driver arrives at the scene, he opens WeChat applet, and the system will retrieve the GPS location information of the driver. If the car has entered the electronic fence, it will automatically enter the queuing sequence and queue according to the name of the goods and the rules required by Party A.
5. Call management: If the vehicle is allowed to enter the factory, WeChat applet will push the prompt message to prompt the vehicle to enter the factory.
6. Access Control Management: When the driver arrives at the door, the outdoor ID card reader and the two-dimensional code or license plate identifier will automatically read the vehicle information. If the system retrieves the vehicle information legally, the gate will be lifted and the vehicle will enter the factory.
7. One-time weighing: 1) When the weighbridge is idle and the vehicle travels to the weighing end, the system will automatically read the vehicle number and retrieve the vehicle dispatch information. (If the vehicle is a temporary vehicle, select the temporary weighing type when the vehicle is dispatched, and read the vehicle number to obtain the dispatching information by the identification of the vehicle number when the vehicle is loaded)
2) The license plate identifier identifies the license plate number of the vehicle and compares it with the vehicle dispatch information. If the vehicle number is the same, the barrier will lift the vehicle and weigh it.
3) The vehicle is completely weighed and does not block the infrared positioning system. The system determines that the weight is stable, automatically saves the weight and captures the picture.
4) The outdoor LED screen displays the vehicle number, weight, unloading area and other field information (optional), and the voice prompts the driver to put down the weight
5) The front gate of the weighbridge is lifted, and the vehicle is weighed down.
8. Secondary weighing: the driver weighs the gross weight on his own. The driver weighs the weight on his own. The system automatically reads the information of the car and retrieves the primary weighing information of the car. If the information is not missing, the weight will be automatically saved and the receipt weighing list will be printed (optional). (Refer to one-time weighing for the operation process)
9. Generate net weight: calculate the net weight instantly after secondary weighing, save the weight, calculate the net weight according to the weight of hair and skin, and prompt the driver with Chinese character screen and voice.
10. Weighing List Printing: After the second weighing is completed, the printer set up in the weighing room or gate will automatically print the weighing list, and the two-dimensional code for this weighing will be invalid.
11. Vehicle leaving the factory: when the vehicle arrives at the exit, the driver gets off the bus and takes the pound list, the system automatically identifies the vehicle, the gate lifts the vehicle leaving the factory, and the information of this weighing and dispatching the vehicle is invalid.
System Module Description
1.Tengyu A8 Informationmanagement platform
Tengyu A8 information management platform is the core of one-code communication system and a large-scale customer management platform. The platform adopts B/S web page architecture, which can be accessed by Internet network and is not limited to the number of users (the factory needs fixed IP for login operation of personnel outside the factory). The system sets strict access rights according to user roles, cooperates with hardware equipment to ensure data confidentiality and security, and the background data is transmitted to each subsystem in real time, to achieve information sharing and seamless docking between modules. The staff of the unit add order plan to the contract management module; Add car dispatch information to the car dispatch management module (or WeChat applet) to realize the pre-information transfer work such as order plan transfer and car dispatch (logistics management).
Tengyu A8 information management platform can be subdivided into functional modules such as information query, information summary, financial management, contract management, car dispatch management, decision management, customer information management, user management, log management, etc. Function modules can be flexibly set according to site requirements. In addition, the entry type and format of information under each function module can be flexibly selected. The function of this project module is described as follows:
1,contract management module:
Add 1.1 Contract and Plan: Sales Department or Finance Department adds contracts and plans on the management platform (the contract approval function of Finance Department can be added), and vehicles can be dispatched only after adding contracts (approved). When customers dispatch vehicles, they can be dispatched by associated contracts.
1.2 additional contract: when the contract is about to end, or the customer adds a new contract (planned order), the relevant personnel of each department can directly add the contract after the contract.
1.3 Contract Management: can modify, add, deactivate and append contracts or plans.
1.4 unit price management: unit price can be set for multiple items in the same large contract. When the price fluctuates, the timing price adjustment can be set for a single item, which is convenient for enterprise management.
1.5 contract log management: all operations of contracts and planned orders are recorded in operation logs, which strictly manages contracts and facilitates traceability operations.
1.6 Prevent pulling goods beyond the contract: when the staff sends the car, the pre-installed amount or load amount shall be added. at this time, the system will automatically calculate the remaining amount of the contract. when the remaining amount of the contract is insufficient, the customer will be prompted that the remaining amount of the contract is insufficient. please contact the staff and prohibit the car from sending.
1.7 Credit Limit: a credit limit can be set for a single customer, allowing them to pull goods beyond a certain amount of the contract (which can be operated by authorized personnel).
1.8 contract review: after the contract is added, the financial department (or a special person) will conduct a unified review to check the correctness of the contract plan before it takes effect (optional)
2. Dispatch management module:
2.1 Add car dispatch: Staff log in their respective accounts in the car dispatch module of BS management platform or WeChat applet car dispatch module, and enter the car dispatch information vehicle information (including driver's name, telephone number, ID card number, license plate number,Pre-installedQuantity, number of axes, name of goods, specification, original weight, etc.), and associated contract plan.
Automatic control of 2.2 contract margin: after entering the load, the system will automatically calculate the contract margin. If the contract and plan cannot meet the pre-installed quantity of the car, it will prompt the customer that the margin is insufficient and contact relevant department personnel for handling. The operation system of this dispatch is not allowed to save.
Effect: The contract control work will be done in advance to prevent the problem from being found after the vehicles enter the factory and affect the on-site work efficiency.
2.3 car dispatch audit: after the customer (driver) adds the car dispatch successfully, the car dispatch enters the audit state, the business personnel or the person in charge of each department check the car dispatch information, check the authenticity and validity of the information, and the audit can take effect. (Optional)
2.4 Dispatch information management: if the dispatched vehicle changes, the person in charge of each department of the unit can modify, deactivate and delete the dispatch information (add details according to requirements) to deal with sudden changes.
2.5 vehicle inquiry: which work link the vehicle is currently in can be displayed, which is convenient for the staff to master and manage the vehicle logistics.
2.6 the effect of dispatching vehicle module: the logistics vehicle information is registered in advance, reducing the on-site registration time;
The management of over-contract pulling is controlled in the dispatch link to prevent the on-site work efficiency from being affected after the on-site over-contract;
The source overload information is entered in advance, and after the vehicle is weighed twice to produce a net weight, the overload is treated in combination with the pre-installed quantity and the number of axles (load).
3. Query Summary Module
3.1 staff of each department of the company can select different fields according to their requirements to perform universal query and summary, and the report content required by each department can be directly exported. 3.2 field selection is divided into two parts
Part: Select all fields required for the report (more than 20 fields, such as purchase, sales, unit, goods name, car number, gross weight, tare weight, etc.)
Part: Select the main filter field and add multiple filter criteria, such as company name and goods name fields to filter query and summary.
graphical data analysis
2. electronic fence management andVehicle queuing system
1. Electronic fence: Set a fixed virtual area on the map, and whether the vehicle enters the fixed area according to the GPS positioning of the mobile phone WeChat.
2. Automatic queuing: When the driver arrives at the parking lot, he opens WeChat applet and logs in to his account number. The system reads the GPS signal of the driver and detects that he has entered the specified area and has the vehicle dispatch information, then the vehicle automatically enters the queue.
3. Queuing rules: queue according to GPS positioning time, queue according to the name of the goods, set the maximum number of vehicles in the factory area, and set the maximum number of vehicles under a single goods name.
4. Queue query: The driver opens WeChat applet and logs in to the account to query the current queue sequence.
5. Call management: The large queuing screen displays the queuing sequence and queuing status, and WeChat applet pushes the prompt into the factory.
6. Limit on the number of vehicles in the factory: Due to the limited space in the factory area, the number of vehicles is limited according to the overall vehicle capacity in the factory area and the maximum vehicle capacity under each cargo name. If one vehicle in the factory leaves the factory, new vehicles will be allowed to enter the factory to ensure the efficiency of vehicle logistics and will not cause vehicle congestion in the factory.
7. Special treatment: for special vehicles or emergency vehicles, there is no need to queue up or set priority to enter the factory (set by the authorized administrator)
8. Achieve the effect: reduce the queuing time of drivers and improve the current situation of road congestion outside the factory area. Improve the efficiency of vehicle logistics in the plant. Improve driver satisfaction and viscosity.
3. access control system
The access control system identifies and checks the vehicles according to the background information flow. The system hardware includes outdoor electronic tag reader, gate, anti-smash radar and so on. The specific process is as follows:
1. Self-service card swiping: The vehicle number has been allowed to enter the factory. When the vehicle arrives at the door, the electronic tag reader will automatically read the vehicle information or the vehicle number will be automatically identified.
2. Vehicles entering the factory: If the weighing two-dimensional code of the vehicle is valid and the queuing sequence is legal, the gate will be automatically lifted and the vehicle will enter the factory. If the information is wrong,
If the road brake bar is not lifted, the driver will go to the security room for treatment (special circumstances can be released manually, and the system will automatically record).
3. Vehicle leaving the factory: if the weighing list is printed and the process is complete, the driver will drive to the door, the system will automatically read the electronic tag or the vehicle number for automatic identification, and the system will verify whether the vehicle process is complete. If the vehicle is legal, the system will control the gate to lift and the vehicle leaves the factory.
4. unattended weighing system
The unattended weighing will be modified on the basis of the existing truck scale.
Unattended weighing scene renderings are as follows:
The system has several major functions as follows:
Infrared anti-cheating function
Automatically detect the weighing condition of vehicles. For vehicles that are not completely weighed or weighed, the infrared positioning system will give an audible and visual alarm, the software will automatically lock, and the system will prohibit vehicle weighing and metering.
This set of infrared positioning system belongs to the fourth generation of products. Not only does the infrared beam adopt 60 m double beam, with nearly 20 times margin and strong penetrating power. Even if it is not wiped for a long time or there are large pieces of dust, it will not affect the normal use. At the same time, an auxiliary warning lamp is added. If the infrared beam is abnormal, the warning lamp will give an alarm to facilitate timely maintenance by maintenance personnel. The pole adopts 1.5mm thick hot galvanized steel pipe, which is not only prevents rust and corrosion, at the same time, the height of 1.5m makes the infrared positioning system beyond the height of the wheel and facing the carriage, which can more accurately position whether the vehicle is completely weighed. Embedded design, more stable, dust-proof and anti-damage. The field use effect diagram is as follows:
Intelligent voice broadcast function
The system automatically reminds the driver to adjust the parking space according to the weighing condition of the vehicle. When the weight of the vehicle is blocked, it will prompt "the infrared is blocked, please drive forward", when the weight is unstable, it will prompt "the weight is unstable, please wait a moment", when the weight is stable, it will prompt "the current weight is XXX, the weight is saved, please take the card to lower the weight", and voice prompt "the planned quantity is insufficient, please call the staff" for the vehicles that are not enough to receive or deliver the goods ", the completion of the measurement prompts the vehicle to lower the scale.
Vehicle capture function
The system monitors the weighing site in real time, captures pictures of the measuring vehicle, saves the weight and automatically captures a group of photos, associates with the weighing record, and automatically uploads video data and picture data. The car number identification system automatically identifies the car number while saving the weight by docking with the software, and compares it with the car number registered by the system.
LED external display function
According to the measurement information of the vehicle, the system displays the information of the gross, skin and net weight of the vehicle, and prompts the area for loading and unloading materials according to the system settings.
The system can also display the number and information of vehicles in various states such as entering the factory without weighing, completion of primary weighing, confirmation of received (delivered) goods, completion of secondary weighing, etc. according to the information of vehicles circulating in the factory.
The weighing process of the system is as follows:
One-time weighing process:
1. When the weighbridge is idle and the vehicle travels to the weighing end, the system will automatically read the vehicle electronic tag and retrieve the vehicle dispatch information. (If the vehicle is a temporary vehicle, select the temporary weighing type when the vehicle is dispatched, and read the vehicle number to obtain the dispatching information by the identification of the vehicle number when the vehicle is loaded)
2. The license plate recognition instrument recognizes the license plate number of the car and compares it with the car dispatch information. If the car number is the same, the barrier will lift the car to the weight.
3. The vehicle is completely weighed and does not block the infrared positioning system. The system determines that the weight is stable, automatically saves the weight and captures the picture.
4. The outdoor LED screen displays the vehicle number, weight, unloading area and other field information (optional), and the voice prompts the driver to weigh down
5. Lift the road brake at the front end of the weighbridge, and weigh the vehicle.
Secondary weighing process:
The driver weighs the gross weight by himself unattended, the driver weighs the weight, the system automatically reads the electronic label of the car, and retrieves the weighing information of the car at one time. If the information is not missing, the weight will be automatically saved and the weighing list will be printed. (The operation process refers to a weighing).
Note: 1. When weighing, the system automatically controls the plan, that is, the current weighing data is compared with the planned margin of the order. If the planned margin is exceeded, the weighing will be rejected and the driver will be prompted. You can also set a credit limit to allow the vehicle to exceed a certain range.
2. When the vehicle is tare weighing, the system can compare the average value of the tare weight of the vehicle recently weighed with the tare value taken this time. If it exceeds the allowable range, the system alarms and does not save the weight.
3. Source control: the net weight of the vehicle is compared with the load of the vehicle. If it is overweight, it is forbidden to weigh and voice prompt the driver.
5. silo matching cargo name quantitative loading
1. Interconnect with the existing loading control cabinet through I/O instructions.
2. When the driver reaches the designated silo for loading, the system will automatically identify the electronic label, match the name of the goods, and the vehicle will enter the bottom of the warehouse.
3. Detect the parked position of the vehicle through the infrared light curtain set on both sides of the lane, start loading from the front of the carriage, the staff will determine the parked position of the vehicle through monitoring, and click the unloading button (or automatically)
4. The blanking port is equipped with an infrared/laser ranging tool, and the blanking degree is determined according to the height of the carriage registered when the car is dispatched. When the material is full and the goods are fast, the driver is prompted to move forward through an electric bell or traffic light, or the driver observes the loading process through a convex mirror, and continuously moves forward to adjust the position of the vehicle. An electronic alarm bell can be added, and the operator can click the bell button to remind the driver to operate normally.
5. According to the pre-loading quantity system of the vehicle, the blanking port is automatically controlled to stop blanking, and the blanking port of the bulk machine is raised.
7. After loading is completed, the system will prompt the Chinese character screen, voice or traffic light, and the vehicle will weigh down and drive out of the warehouse bottom.
8. Feeding software (a set of software to control multiple silos)
When the driver arrives at the silo, the outdoor two-dimensional code recognition instrument or license plate recognition instrument will automatically recognize it. The system will retrieve the name of the goods in the card and the information of the pre-loaded quantity (if the information of the goods name matches, the blanking is allowed). The staff will check whether the vehicle is parked as required through monitoring. The staff will click the button to start blanking. The system interfaces with the silo weighing system and controls the bulk machine to automatically shut down according to the vehicle.
System features
1. automatic weighing, unattended
In the whole weighing process, electronic tags, license plate recognition instrument and other hardware systems are used to realize unattended automatic weighing. The system reads electronic tag information or automatically recognizes the car number. The system automatically calls up the car number, unit, goods name and other information. The infrared positioning system judges that the car is completely weighed. After the software judges that the weight is stable, it automatically saves the weight and captures photos. The weighing information such as car number, goods name and unit, information such as weight is displayed on a large outdoor screen for the driver to compare. At the same time, the voice prompt system reports the current weight and prompts the vehicle to weigh down. The traffic light status indicates that the vehicle weighs down. The whole process realizes unmanned operation, intelligent automatic control, improves the weighing speed, and reduces possible cheating behaviors caused by personnel intervention.
2. strong anti-cheating measures
-
The weight data is collected directly from the instrument and cannot be input manually or copied and pasted to ensure that the data is accurate;
-
The black box function automatically records the weight information of each car to prevent the driver from colluding with the operator and not operating when the car is weighing;
-
On/off recording function, automatically recording the time of each on/off operation personnel to prevent individual personnel from cheating by means of on/off operation;
-
Log management function, authorized personnel can modify the relevant data in the database, but after modification, the software will automatically generate a modification record, keep the modification time, modification personnel, modification content, etc;
-
Real-time monitoring is carried out through the cameras installed around the weighbridge, the weight is saved and a group of photos are automatically captured at the same time, which are associated with the weighing record. When querying the data, the software automatically fetches the gross weight photos and tare photos at the time of weighing for comparison, so as to prevent cheating such as the return of the cart weighing, the return of the cart weighing the cart and the return of the cart weighing the cart;
-
The system can set the tare weight fluctuation range. If the tare weight of the vehicle exceeds the set range of the system, the software will automatically warn and cannot weigh it;
-
The infrared positioning anti-cheating system prevents the vehicle from being weighed incompletely or the front and rear vehicle pressure scales;
3. strict permission management
For example, weighing authority, parameter setting authority, query statistics authority, data supplementary recording authority, weighing list authority, data modification authority, etc., operators can be added, operators can be deleted, permissions can be changed, etc., which are not only strictly managed to ensure the safety of data, but also humanized settings to handle abnormal situations.
4. flexible print formats
The system has more than a dozen print formats can be selected, and can achieve multiple printing. Can realize the filling type printing, can greatly improve the printing speed. Users can also design their own print format.
5. dual database structure
Tengyu weighbridge weighing intelligent management system uses a dual database scheme, that is, the use of two sets of databases, a local database, a server database. When the network is interrupted or network failure occurs, the local database is used without affecting the normal weighing. When the network is running normally, the server's database is used, and all local data is synchronized to the server in real time, which can borrow the advantages of the network and is not affected by network interruption.
6. Universal Query Summary
According to the needs of enterprises, you can query the daily summary, monthly summary, annual summary, report printing of multi-condition combinations such as car number, goods name, unit, etc. in any time period at any time, and you can export EXCEL forms. The system itself has a variety of report formats for use, and can also be customized to design according to user requirements.
7. fuzzy retrieval function
Preset phrase information such as receiving unit, shipping unit, goods name and other information input name initials, the software according to the letter to match, faster call up the corresponding information. Software screenshots are as follows:
8. graphical data analysis
Based on the original universal query summary function, the software can automatically generate graphical analysis reports, such as column charts, line charts, pie charts, etc., for relevant leaders to make more intuitive decision-making analysis. Software screenshots are as follows:
9. rigorous program management capabilities
Sales Department or Finance Department can add orders for plan management. When weighing, the plan can be deducted by amount or weight. If the weighing data exceeds the planned margin, the system will prompt you not to weigh, or set an over-plan limit. The system will automatically generate a negative plan. Details can be queried by criteria and print and export are supported. The plan of each company can divide large orders into multiple small orders, and at the same time, the unit price information of goods of different specifications in different companies can be added. The software can automatically match and call. In addition, the software adds a perfect plan log, appending plans, invalid plans and all other operating software are automatically recorded. At the same time, the software can carry out more detailed and perfect management of plan management, data modification or supplementary recording, the software can automatically call up the plan information corresponding to the vehicle record, automatically deduct the weighing record of the vehicle, and automatically update the plan margin. The plan control process is as follows:
Software screenshots are as follows:
10. universal weighing instrument interface
The software can be equipped with truck scales, rail scales, etc. The software has a variety of interface programs and can be equipped with various well-known weighing instruments in China, such as Yaohua XK3190 A1, Yaohua XK3190 A9, Yaohua XK3190 D9, Yaohua XK3190 D2, Toledo 8142-07, Toledo 8142-08, Heng Tian 9800B, Heng Tian 9800C, XK-3110-C, Japanese, K3800 points, Heng Tian, lay the foundation for the enterprise to expand the electronic scale in the future; It can make the enterprise only set the parameters of the software after replacing the weighing instrument, which has wide applicability and completely relieves the user's worries.
11. Powerful device interface
The interface between the (I) and the LED display screen: not only can the digital screen be matched to display only the weight information, but also the Chinese character screen can be matched to display the weighing information such as "goods name", "specification", "car number" and "weight" more intuitively.
The interface between the (II) and the controller: the controller can be matched to realize the control of "road gate", "traffic light", "infrared", "ground induction coil", etc., and realize the unattended intelligent automatic control of the weighing process.
(III) interface with intelligent swipe system.
XII. Remote Centralized Monitoring and Management
It can realize remote centralized management. For enterprises with multiple branches of a company, it can remotely monitor the working conditions of the weighing room through the wide area network, inquire and summarize, issue plans and other management. The system can connect each weighing room and the leadership office, and after networking, the weighing data can be shared, and the leaders can synchronize the data and images of each weighing room in the office.
Previous Page
Next Page
Tengyu weighing instrument, the choice of quality

Perfect service management guarantee mechanism
It covers pre-sales consultation, in-sales follow-up and after-sales support to ensure that customers can receive timely and professional services at all times.

Strong R & D capability
The company is equipped with a technical center and has a high-quality technical development team, of which 80% are bachelor's degree or college degree or above, and 35% are all kinds of professional and technical personnel.

Strong technical equipment strength
The introduction of international advanced level of key technology and equipment, with CNC machining center, CNC lathe, CNC laser cutting machine, CNC plasma/fire cutting machine, CNC bending machine, vacuum heat treatment furnace and a number of modern industrial technology and equipment; and equipped with shot blasting production line, large scale coating production line and other advanced equipment
Previous Page
Next Page
Related Products
Immediate Consultation
If you are interested in our products, please leave your email, we will contact you as soon as possible, thank you!